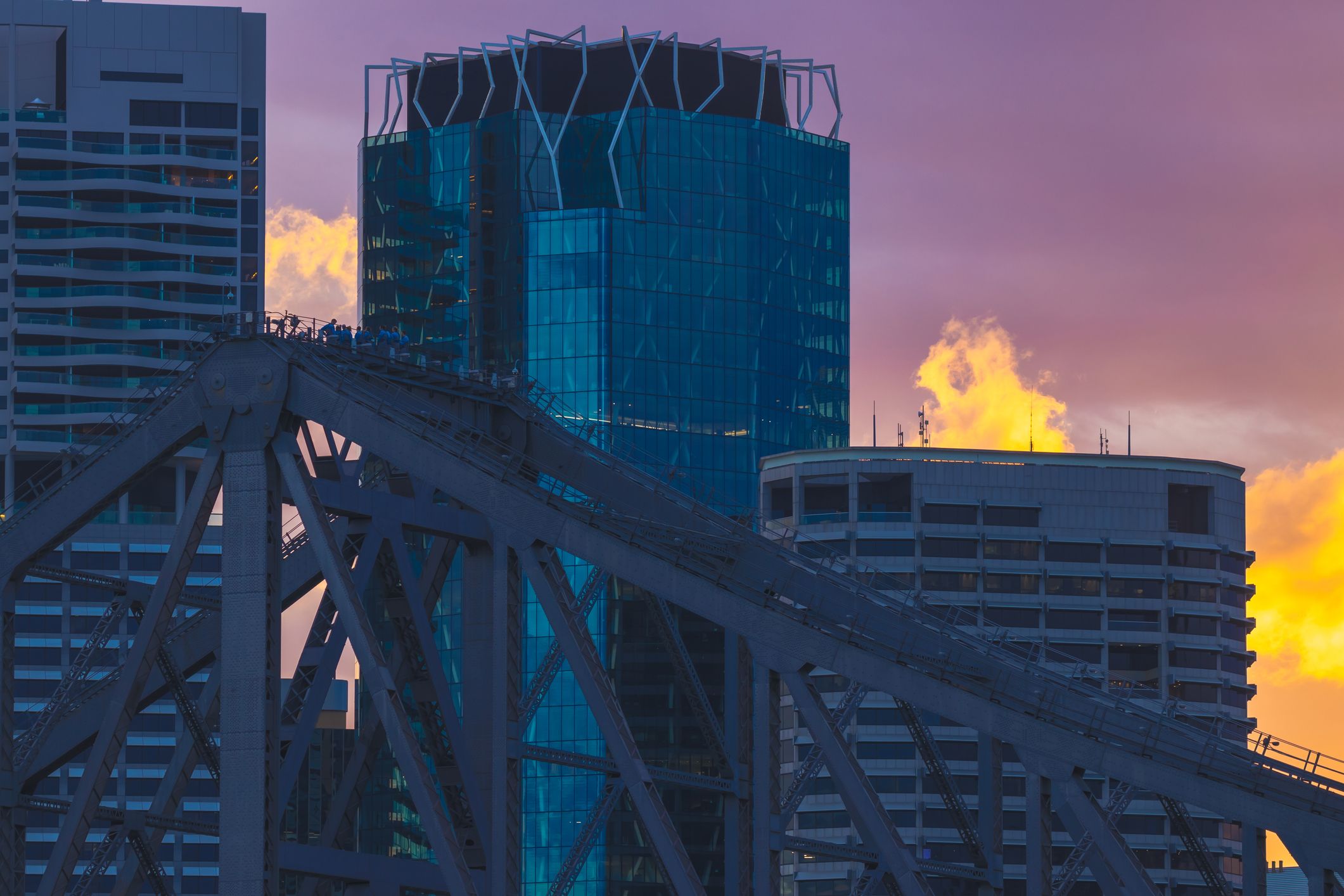
Rethinking the currency of construction productivity
In my last article, I shared some reflections on the recently published RICS report titled “RICS Construction productivity report 2023” and concluded with questions about: why the construction industry doesn’t measure productivity as well, or as regularly, as it should; and how organising and structuring data and systems is a significant challenge for a lot of organisations.
In most businesses financial metrics (e.g. profitability) are the de facto measure of productivity. However, these are misleading metrics and productivity measures need to focus on hours as the currency rather than financial information which tends to be polluted with numerous factors that are not productivity related (a person’s opinion, market inflation, design development etc).
This article will explore the challenges to shifting our thinking to use hours as the currency of productivity measurement, rather than financial metrics such as profitability.
Do you know your production rates?
Effective productivity measurement starts with knowing the production rates assumed in the price you have agreed with your client; in simple terms this is the rate of progress you need to achieve to deliver profitably.
There are numerous industry terms for this, but I will refer to it as the baseline production rate. It is rate at which you estimate it will take to perform a task and it is multiplied by factors such as the number of operatives rate, the operative cost rate, and the quantity of work to be performed. This calculation delivers a rate which is proposed and negotiated with the client in the agreement of a contract sum.
It surprises me how few people know the production rate that forms the basis of their contract sum, and therefore the budget. When I ask the question, I am either met with a blank look or there is a “that would be a useful piece of information” lightbulb moment. There are sometimes reasons for this, maybe as a main contractor you rely on subcontract estimates, but these rates are a critical baseline metric so, if you can’t access them, you should form your own judgement.
If you don’t know the baseline production rate, then how can you say you are measuring performance correctly? And, as a quantity surveyor, how can you say that you are picking up entitlement to time and cost at the time the event occurs. Or are you waiting for someone to tell you it has occurred before you do something about it? Always be ahead of the issues, and everyone else.
Data and systems
Whilst knowing the baseline is key, it becomes difficult to measure performance if your cost and programme data are not delivering information in a way that allows you to calculate performance.
Your source of cost data for cost to date will be the finance system and, more than likely, a spreadsheet for forecast cost. What you will often find is the data structure of this information, particularly the finance system, will not be structured in a way that allows you to calculate an actual or forecast production rate. This is because the data you need (operative quantity, type, hours worked etc) will be splattered across numerous cost codes and / or require to you dig deep before you can extract the information you need.
The challenge of calculating an actual or forecast production rate, to compare against budget, is compounded by the data structure of programme information often being different again (to the cost data structure and the estimate data structure). What you need to know is the quantity of physical work performed so that this can be worked back to a unit per hour (e.g. m2/hour, tonnage/hour etc). You will sometimes find progress measured as a percentage which is too subjective to measure progress, or that the programme isn’t resource loaded (or if it is resource loaded it doesn’t align with the basis of the agreed price).
Each one of these issues is a barrier and makes productivity measurement that bit more impossible to do.
Business intelligence
I work with, and know of, several companies who are trying to do things differently. They want to find a way to integrate their data and systems and automate the process of translating the data, rather than relying on their teams to do it manually. The logic is simple; automate non-value-add tasks and allow people to focus on value-add problem solving.
One of the challenges I sometimes see is being fixated with making the interface “dashboard” look good. There is only so much value to be gained here before the nitty gritty needs to be done. Ultimately, if the wiring between your analytics and data is not right, it doesn’t matter how pretty the interface “dashboard” looks like, it will not yield the insights you need (and often people in the background will manage the inputs to convey their preferred message).
There isn’t, as far as I have seen, a ‘silver bullet’ solution to this challenge where one piece of software can be placed over your data and seamlessly give you the insights you need. This is because most business have invested in a system for a particular purpose and have not stepped back to think about how one system works as part of a business network.
This isn’t a reference to the network of connecting computers but rather how the planning finance, estimating, and document management system work together to produce business information.
Final reflections
I am certain that using hours as the basis of productivity measure will go some way to unlocking the challenge we have with measuring productivity.
This article provides some insights into the challenges with achieving this and hasn’t even touched on the biggest challenge which would be business culture. However, hopefully it has given you some food for thought that you can apply to your own working environment to improve the way you measure productivity.
I have written a few articles on construction activity and plan to round off this mini-series with a more light-hearted article next week so keep your eyes peeled for that one.
Back to insights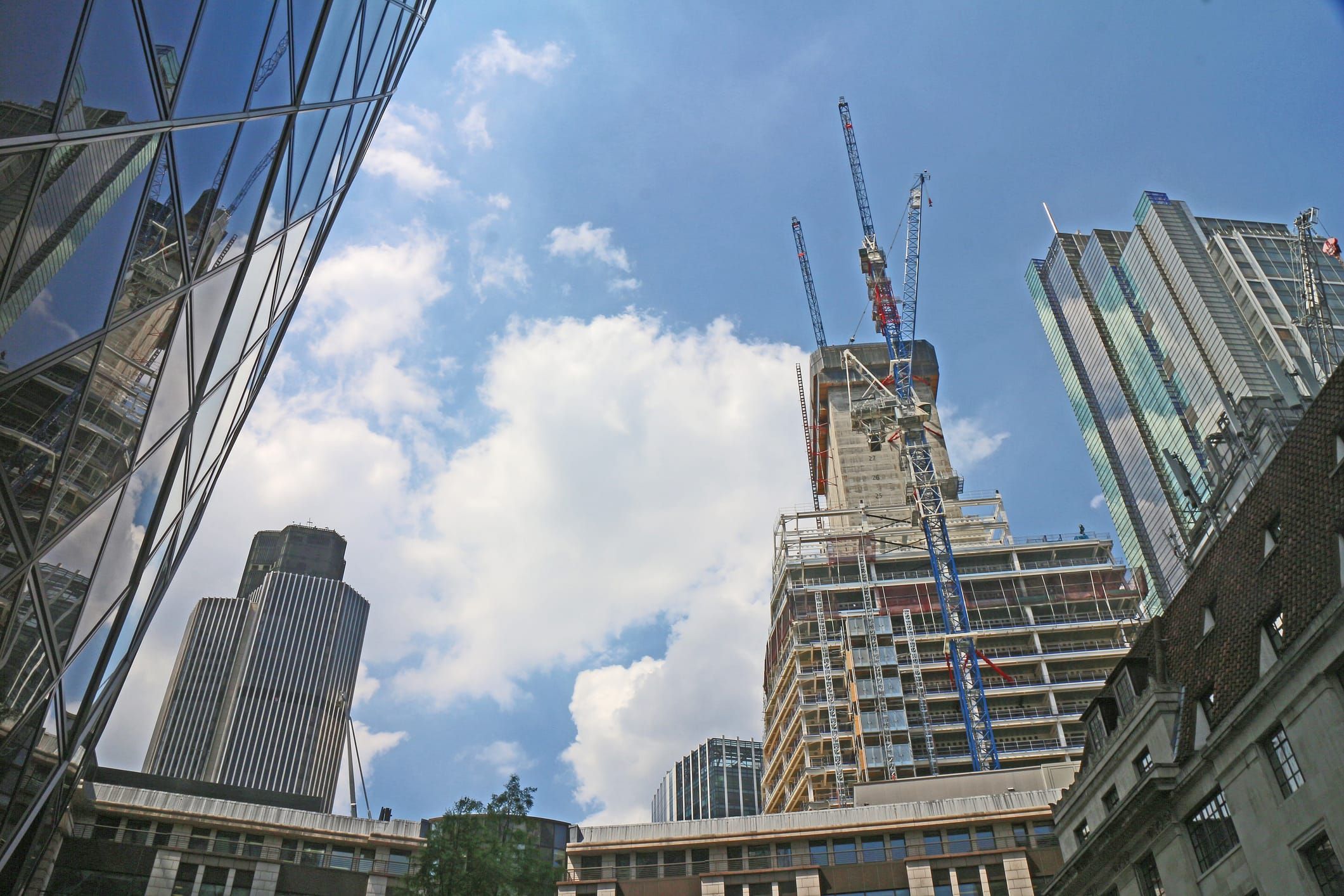
THE SCIENCE OF QUANTIK™
Publications
We publish insights through our LinkedIn newsletter, titled “The science of Quantik”, which are light bites of information covering news and insights relating to the construction industry and quantity surveying.
LinkedIn