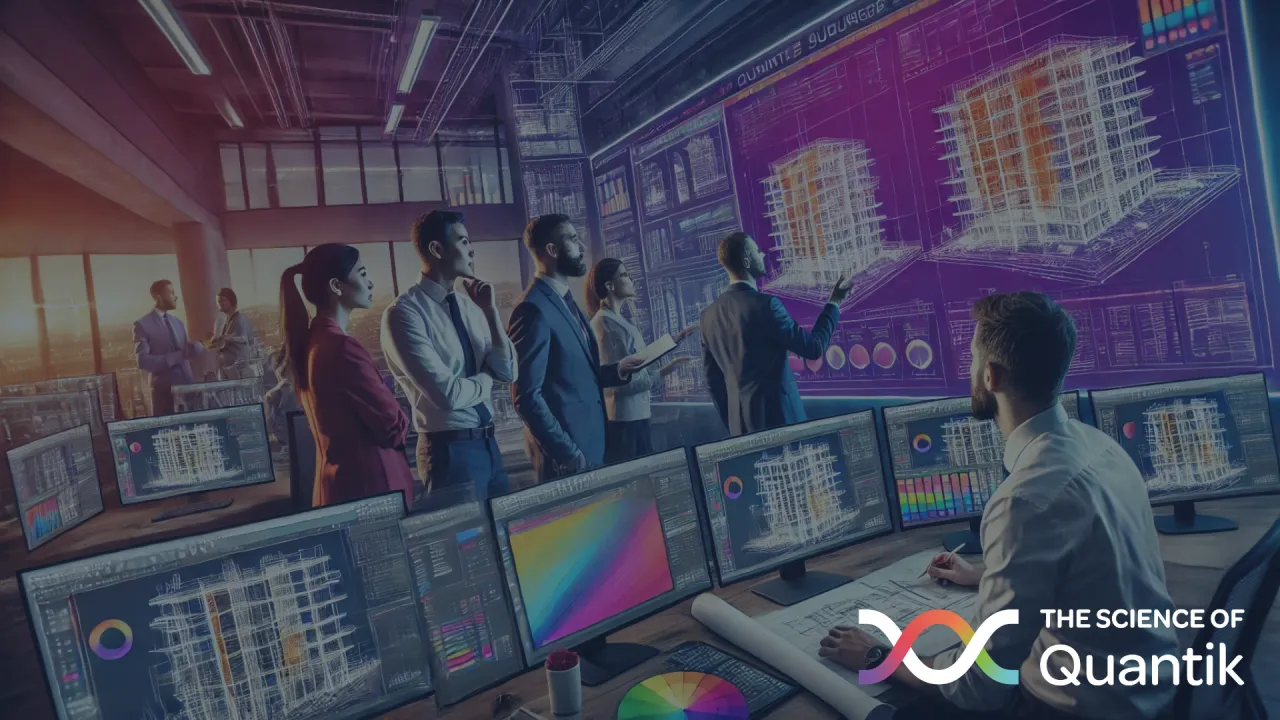
Intelligent use of technology: design change management
In this fourth article, I follow on from my colleagues to share my experience using @Bluebeam’s drawing overlay feature to identify and manage design change.
Nothing is certain in life except death, taxes and change on a construction project!
As a quantity surveyor, one of my primary duties is to understand change and ensure any additional time and/or money is recovered. This can be challenging because change is occurring all the time, the relevant information tends to be scattered across a project, and construction projects tend to be fast-paced with demanding clients and stakeholders.
It is possible that, without putting in place appropriate commercial controls, change will be missed, and the financial consequences are severe because cost is incurred without revenue and failure to recover time results in increased time-related costs and exposure to damages.
The challenge of identifying design change and the cause of that change is not helped by the way design information is shared and coordinated in a digital model. This is how design change happens on a construction project, and whilst I would love to have drawings with revision numbers to pick up change, I acknowledge that it is both time-consuming and uneconomical to continuously print out the drawings and perform a ‘traditional’ comparison.
To help me with this challenge, I used @Bluebeam’s overlay feature, which enabled me to see changes as the feature highlights design changes and provides information in a way that I could prepare quantity take-offs, understand changes in scope/materials, and prepare and issue cost estimates efficiently.
My experience
I was working on a retail project which, given it was a refurbishment project that had to be completed in a very short window, was challenging. There are multiple revisions of design information prepared both during the tender and construction periods.
I used the overlay feature to control design change on this project. When a change was made that might impact the budget, I flagged the issue with the design team to understand more about the change and either seek to influence the cost implication of the change or identify the source of the change and recover additional time and/or cost.
The tool allowed all design team members to collaborate and make notes on design information regarding changes. This meant items were not missed and scope changes were picked up in their entirety because the design team member would describe any related builders work or other impact that the change may have. I tend to be good at picking up those consequential impacts, but it was reassuring to have that information in case something was missed.
What did I learn?
Traditional take-off methods are outdated and are no longer suitable for the commercial control of design change. The overlay tool provided information to me in a way that focused my attention on the change, and I didn’t have to compare two different printed drawings to find the change. This is not only time-consuming, but there is an increased chance that a change is missed.
By using a digital tool to manage design change, not only did I save a few trees, but I could also manage design change across multiple drawings at the same time. I could move around the information quickly and efficiently, which meant my time was focused on understanding the change and its impact rather than trying to locate the change.
That said, there can be issues. The software doesn’t always align drawings over one another, resulting in changes being highlighted that are not actually changes. You can’t just take what the overlay tells you and use it, and there is an additional check required to ensure that there is a change. There is an automatic alignment function which is helpful, but it does not always work, so I would recommend the check is required.
When I was dealing with large sets of the drawings, the software could be slow and cumbersome, which, coupled with visual clutter if there are multiple revisions, can impact your time efficiency.
Final reflections
Overall, whilst there were some challenges with using the software, I found it saved me a considerable amount of time and improved my ability to control design change on the project, leading to greater financial control and improved margin certainty.
Whilst it helped me identify the changes, the operation of the software still requires a QS to know what is and is not a change and requires design team members to identify the impact of a change on other building elements. This improves the structure of the information and the efficiency with which it is exchanged between project stakeholders.
This article concludes this mini-series, and next week we will kick off a new mini-series about AI in quantity surveying.
Keep an eye out for that, and, in the meantime, enjoy the rest of your week!
Back to articles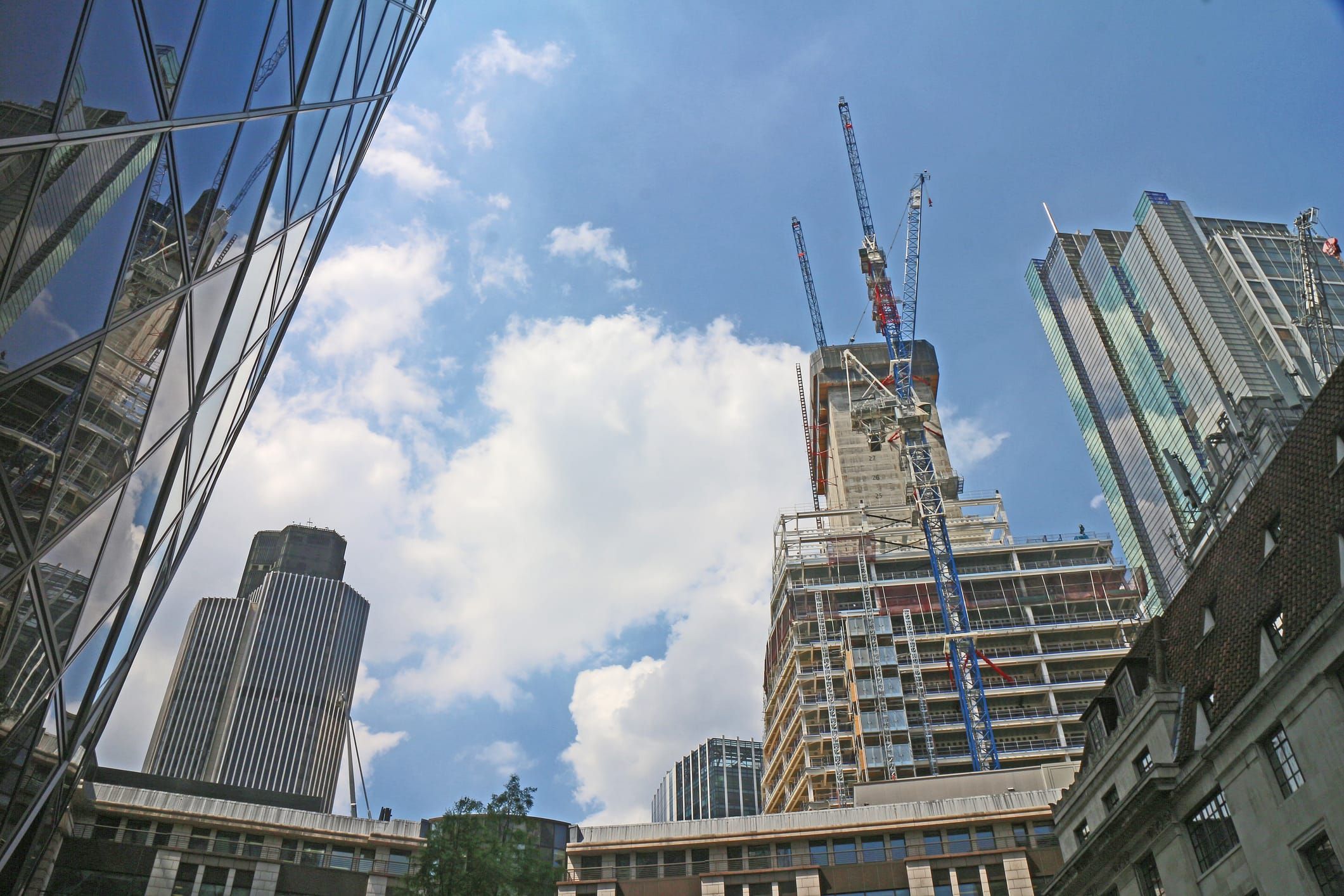
THE SCIENCE OF QUANTIK™
Publications
We publish insights through our LinkedIn newsletter, titled “The science of Quantik”, which are light bites of information covering news and insights relating to the construction industry and quantity surveying.
LinkedIn